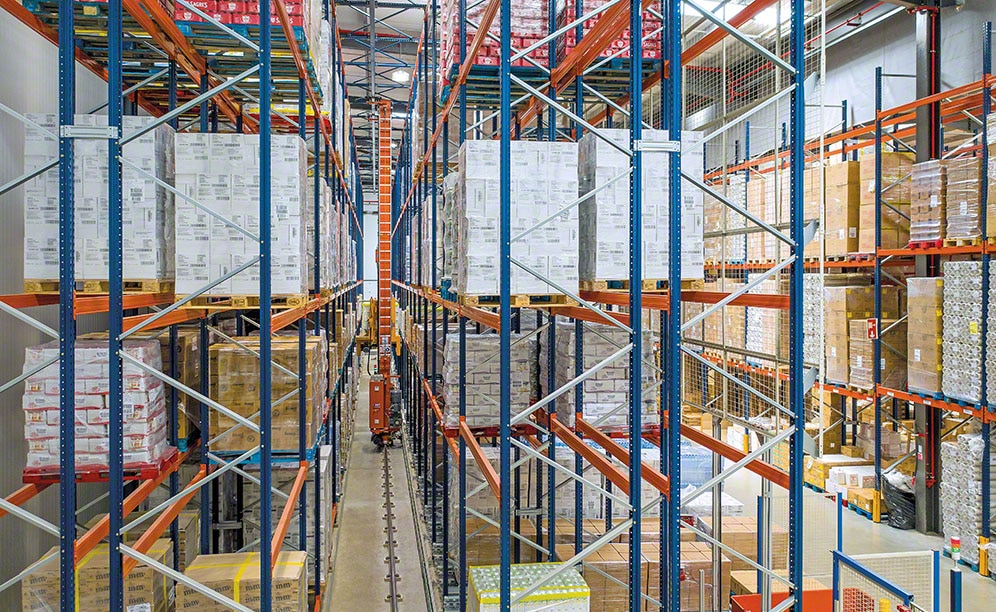
La technologie améliore la productivité, la performance et la consommation énergétique
La chambre de congélation et stockage d'aliments entièrement automatisée d'HAVI
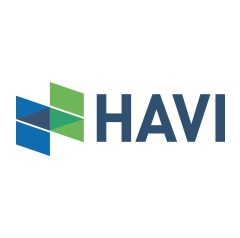
HAVI a inauguré un centre logistique moderne et technologiquement avancé au Portugal, d’où elle approvisionne ses clients portugais du secteur de l’alimentation. Le centre est divisé en trois zones qui fonctionnent à température ambiante, réfrigérée et à -20 °C. Mecalux a fourni tous les systèmes de stockage : deux magasins automatiques, des rayonnages à palette, des rayonnages drive-in et des rayonnages avec Pallet Shuttle. De même, elle a installé Easy WMS, le logiciel de gestion d’entrepôt connecté au WMS d’HAVI afin de contrôler le stock et de garantir le séquencement dans l’expédition de la marchandise.
À propos d’HAVI
HAVI est une multinationale spécialisée dans l’innovation et l’optimisation de la chaîne logistique de marques leaders. Son catalogue comprend des services autour de la logistique, la supply chain et l’emballage mais aussi des analyses marketing. Fondée en 1974, HAVI est présente dans plus de cent pays. Parmi ses clients portugais du secteur de l’alimentation, se trouvent notamment la populaire chaîne de restauration rapide McDonald’s et la marque Portugalia.
L’un des points forts d’HAVI est l’efficacité opérationnelle et l’excellence tant au niveau de ses services, qu’en matière de sécurité et de qualité. Il s’agit d’une entreprise pionnière dans l’approvisionnement de produits aux restaurants qui en ont besoin à un moment précis. Pour ce faire, ses centres logistiques disposent d’un fonctionnement rapide et efficace, qui effectue un contrôle exhaustif de la marchandise en respectant les conditions de stockage appropriées.
Un entrepôt moderne, efficace et durable
Le département technique de Mecalux a de nouveau collaboré avec HAVI afin de concevoir, construire et lancer un centre logistique moderne à Vila Nova da Rainha (Portugal). Ce centre de distribution approvisionne les clients du secteur de la restauration de tout le pays. Les deux multinationales avaient déjà collaboré sur d’autres projets, formant un couple gagnant. Ainsi, par exemple, Mecalux avait déjà installé un entrepôt automatisé pour HAVI à Moscou (Russie) et avait aussi équipé le centre que l’entreprise possède à Lodi (Italie) avec des rayonnages sur bases mobiles Movirack. Avec une surface totale de 10 000 m2, le nouveau centre d’HAVI au Portugal a été divisé en trois zones afin de stocker et de maintenir la marchandise à la bonne température : congélation, réfrigération et température ambiante. Chacune des chambres a une distribution spécifique en fonction des besoins logistiques de l’entreprise, c’est pourquoi, Mecalux a mis en place différentes solutions de stockage et de picking (automatiques comme classiques). Le dénominateur commun de ces solutions est le fonctionnement et la fiabilité au moment de gérer le stock, ainsi que la rapidité que ces systèmes apportent aux tâches de stockage et de préparation de commandes. Véritable référence au niveau technologique, ce centre est également précurseur en termes d’automatisation des processus logistiques à -20 °C.
Les rayonnages à palettes se trouvent dans les trois zones du centre. Le choix de ce système est dû à sa capacité d’adaptation à tout type de charge, de poids et de volume. De plus, l’accès direct facilite la gestion de la marchandise. Aux niveaux inférieurs, les opérateurs effectuent le picking directement sur les palettes à l’aide de terminaux RFID. En revanche, aux niveaux supérieurs des rayonnages, les opérateurs déposent la réserve de marchandise.
Dans la conception de chacune des solutions de stockage, Mecalux a donné la priorité à la sécurité de la marchandise et des opérateurs. En effet, respecter la chaîne du froid des aliments et éviter sa rupture est indispensable. Par conséquent, les accès à la chambre réfrigérée et de congélation sont isolés, ce qui évite les changements brusques de température, les pertes de froid et la condensation.
L’automatisation a également contribué à augmenter la sécurité car 77 % des déplacements des palettes sont entièrement automatisées. D’autre part, elle a contribué à l’amélioration de l’ergonomie pendant la manutention des produits et à réduire l’effort physique. Il convient de souligner que les travailleurs passent moins de temps dans des environnements froids. Outre le gain en qualité de travail, la consommation d’énergie diminue de 10 % car les portes d’accès à la chambre ne sont pas ouvertes aussi fréquemment qu’avant.
Représentant d’HAVI
« Maintenant nous nous adaptons aux changements dans nos activités, nous contrôlons mieux la durée de conservation des aliments et nous sommes plus efficaces dans la gestion des commandes »
La chambre de congélation
Elle est équipée du Pallet Shuttle, un système moderne et automatique, desservi par deux transstockeurs et géré par Easy WMS. Dans cette chambre sont stockées les références à forte rotation, comme les steaks hachés, les pommes de terre, les produits à base de poulet, etc. « La plupart des commandes envoyées aux restaurants sont préparées dans la chambre de congélation », affirme un responsable d’HAVI. L’entrepôt, qui fonctionne à une température de -20 °C, dispose de deux allées dotées de deux blocs de rayonnages ayant une profondeur suffisante pour stocker six palettes au maximum. En tout, elles offrent une capacité de stockage de 2 247 palettes, soit 75 % de plus qu’un système de stockage non automatisé.
Le système Pallet Shuttle automatique optimise l’espace de stockage et réduit le volume devant être refroidi. Cela permet d’augmenter la capacité de stockage, tout en permettant de réaliser des économies sur le coût de l’énergie nécessaire pour maintenir l’installation à une température négative. « Notre objectif était d’améliorer la performance de cette zone tout en améliorant les conditions de travail des employés », indique un représentant d’HAVI.
Le fonctionnement de l’entrepôt est entièrement automatisé dans la mesure où il dispose de deux transstockeurs bi-colonne, qui transportent la marchandise entre les positions d’entrée et de sortie de l’entrepôt jusqu’aux canaux de stockage. À l’intérieur des canaux, la navette motorisée déplace, quant à elle, la marchandise. Tout cela, sous le contrôle d’Easy WMS, qui se charge de contrôler le stock de l’entrepôt. Ce logiciel communique avec le WMS d’HAVI afin de garantir la traçabilité totale de la marchandise, de sa réception à sa livraison aux clients. Un circuit de convoyeurs, qui transporte la marchandise à une vitesse constante de 20 m/min jusqu’à la zone de picking en suivant le principe de « produit vers l’homme », a été installé juste à côté de l’entrepôt. « Nous avons obtenu de meilleures conditions de travail grâce à cette méthode de préparation de commandes », explique un des responsables d’HAVI. Les commandes séquencées par Easy WMS sont préparées indépendamment ou conjointement dans deux postes de picking manuel et un poste automatique, en fonction des besoins de chaque commande. Pour cela, une navette se charge de connecter les trois postes de picking entre eux et de les relier à la zone d’emballage et d’étiquetage.
Le poste de picking automatique est équipé d’un robot anthropomorphique qui manipule des couches complètes de produits à forte rotation (représentant 40 % du volume total des commandes préparées dans la chambre de congélation). Le principal avantage de ce type de machines est leur vitesse sachant qu’il est possible de préparer plusieurs commandes simultanément. Le picking automatique offre rapidité et économie des coûts opérationnels et encore plus dans les chambres de congélation.
Les deux postes de picking manuel reçoivent automatiquement la marchandise des convoyeurs provenant de l’entrepôt ou de la navette, dans le cas où celle-ci est préalablement passée par le robot anthropomorphique. Dans les deux cas, le principe de « produit vers l’homme » permet de réduire les déplacements et d’accélérer la préparation de commandes. À chaque poste, équipé de dispositifs lumineux PTL (pick-to-light), l’opérateur peut préparer de manière ergonomique jusqu’à huit commandes à la fois, ce qui se traduit par une augmentation de la productivité et de la qualité du travail. Au moyen d’un écran, Easy WMS indique aux opérateurs toutes les tâches qu’ils doivent exécuter afin de maintenir le séquencement des commandes : les produits à retirer, la commande dans laquelle les placer, etc. Une fois leur travail terminé, ils le communiquent au WMS en appuyant sur un bouton du dispositif PTL.
Ensuite, la navette collecte les commandes terminées et les envoie à la filmeuse et à l’étiqueteuse. À leur tour, les convoyeurs les conduisent jusqu’à la zone d’expédition de manière séquencée. Cette zone, qui est également à température contrôlée, afin de ne pas interrompre la chaîne du froid, est formée de huit canaux dynamiques de préchargement où les palettes sont classées et regroupées en fonction de la commande ou de l’itinéraire de transport. Respecter le séquencement et regrouper à l’avance les commandes dans des canaux de préchargement permet de gagner du temps et de minimiser les erreurs lors du chargement de la marchandise dans le camion.
Un bloc de rayonnages par accumulation, doté du système Pallet Shuttle semi-automatique, d’une capacité de stockage de 237 palettes, contenant principalement du pain, a également été installé dans la chambre de congélation.
Cette solution, qui optimise aussi la surface de stockage, dispose d’une navette motorisée qui déplace automatiquement les palettes à l’intérieur des canaux. Mais, à la différence du magasin automatique, les opérateurs placent la navette et la marchandise dans le canal correspondant, à l’aide de chariots à mât rétractable.
La chambre réfrigérée
En plus des rayonnages à palettes, Mecalux a installé un bloc de rayonnages par accumulation drive-in de 9 m de haut d’une capacité de stockage de 1 996 palettes. C’est une solution optimale pour stocker des produits homogènes et un grand nombre de palettes par référence, principalement, des tomates, des salades préparées, etc.
Les rayonnages sont formés par un ensemble d’allées de quatre niveaux de hauteur. À leur tour, chaque niveau dispose de rails de guidage des deux côtés, sur lesquels les palettes sont placées. Pour la gestion de la marchandise, les opérateurs pénètrent à l’intérieur des allées, à l’aide de chariots à mât rétractable, avec la charge surélevée par rapport au niveau sur lequel elle sera déposée.
La chambre à température ambiante
Dans cette zone, destinée au ketchup, à la mayonnaise, aux jouets, aux emballages ou aux bouteilles d’eau et autres boissons, se trouve un magasin automatique d’une capacité de 530 palettes, formé par une seule allée dotée de rayonnages à double profondeur, de 10,2 m de haut des deux côtés. Un transstockeur bi-colonne déplace les produits dans l’allée, depuis les convoyeurs d’entrée jusqu’aux emplacements assignés par le WMS.
Au niveau inférieur des rayonnages, 36 canaux dynamiques de picking, qui coïncident avec l’allée de travail, ont été aménagés. Chaque canal peut stocker quatre palettes d’une même référence : une pour le picking et les trois autres servent de réserve. Les opérateurs, au moyen de leurs terminaux RFID, localisent les références qui composent chaque commande et effectuent le picking de la première palette. Lorsque la palette d’un canal dynamique est vide, le WMS ordonne au transstockeur de réapprovisionner ce canal avec la marchandise correspondante. L’avantage de ce système est que les produits nécessaires pour effectuer le picking sont toujours disponibles, ce qui évite d’éventuelles interruptions et des retards dans la préparation de commandes.
Le logiciel Easy WMS : séquencement et contrôle de la marchandise
Les deux magasins automatiques d’HAVI (celui de la chambre de congélation et celui de la chambre à température dirigée) sont pilotés par le logiciel de gestion d’entrepôt Easy WMS de Mecalux. Dans le magasin automatique avec Pallet Shuttle, Easy WMS identifie les articles au moment où ils arrivent à l’entrepôt et leur attribue un emplacement en fonction de leur capacité d’empilage et de leur type. Le système assure une traçabilité totale permettant de connaître la localisation exacte et en temps réel de toute la marchandise.
Le WMS organise aussi la préparation de commandes. D’un côté, il ordonne l’envoi des références requises aux postes de picking et, de l’autre, il indique aux opérateurs les produits qui composent chaque commande.
Easy WMS effectue toutes ces tâches en tenant compte d’une des principales exigences d’HAVI : le séquencement des commandes. Le fait de regrouper et séquencer la marchandise pour l’expédition évite les erreurs, accélère les opérations et permet d’offrir un service plus efficace.
Dans la chambre à température ambiante, Easy WMS indique au transstockeur les différents déplacements à effectuer. Son travail consiste à approvisionner les canaux dynamiques de picking en marchandise au fur et à mesure qu’ils se vident. Easy WMS communique avec le WMS d’HAVI afin de contrôler le stock, de connaître la traçabilité et de séquencer tous les processus du centre de distribution.
La technologie au service des clients
HAVI dispose d’un centre de distribution moderne et technologique performant, conçu pour approvisionner dans les plus brefs délais les restaurants de ses clients. L’automatisation a non seulement dynamisé les flux de l’entrepôt, mais elle a aussi réduit les coûts logistiques et a amélioré le travail des opérateurs. Il convient de souligner que cette installation a permis aux opérateurs d’HAVI d’acquérir de nouvelles compétences.
Les avantages pour HAVI
- Le tri de la marchandise : l’entrepôt est sectorisé en trois zones dans lesquelles différentes solutions de stockage ont été mises en place afin de stocker et de gérer la marchandise en fonction de ses caractéristiques.
- Le séquencement des commandes : Easy WMS se charge de séquencer les commandes préparées et de les envoyer à la zone de préchargement, où elles sont classées en fonction de la commande ou de l’itinéraire de transport.
- La technologie et la sécurité : l’automatisation permet à l’entrepôt de répondre aux exigences indispensables en matière de sécurité de la marchandise et des opérateurs.
- Un lieu de travail gratifiant : HAVI a récemment modernisé son environnement de travail, en le rendant plus attrayant pour les opérateurs et en leur garantissant la possibilité d’acquérir de nouvelles compétences grâce à l’utilisation de nouvelles technologies.
Centre de distribution Portugal: Magasin automatique à température ambiante | |
---|---|
Capacité de stockage: | 530 palettes |
Dimensions des palettes: | 800 x 1 200 mm |
Poids max. des palettes: | 1 000 kg |
Hauteur des rayonnages: | 10,2 m |
Galerie
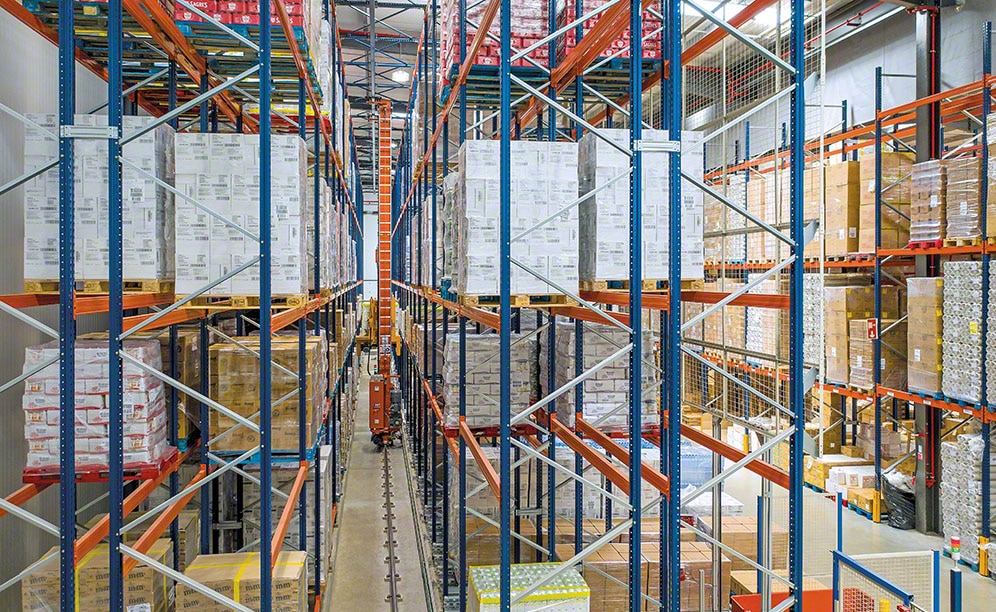
Le système Pallet Shuttle avec transstockeur d'HAVI au Portugal
Demandez conseil à un expert